structured
problem
solving
structured problem solving
Link Copied
- March 18, 2024
RCA is used in many areas like engineering, making things, healthcare, computers, and making sure things are good quality. It helps companies understand why bad things happen, like when machines break, products don’t work right, accidents occur, mistakes are made, or customers aren’t happy.
Root Cause Analysis typically involves the following steps:
- Define the problem: Clearly state what issue or event needs analysis and set the boundaries of what will be investigated.
- Collect data: Gather all relevant information and data related to the problem, including incident reports, documents, interviews, observations, and other sources.
- Identify the immediate causes: Figure out the factors or events that directly led to the problem. These are like the symptoms of the issue.
- Identify the root causes: Go deeper to find the underlying factors or systemic weaknesses that contributed to the immediate causes. Root causes are the fundamental reasons why the problem happened.
- Analyze causation: Use different techniques, like asking “why” five times, using fault-tree analysis, or making fishbone diagrams, to understand the cause-and-effect relationships leading to the problem. This helps uncover multiple layers of causation.
- Develop corrective actions: Based on the root causes identified, come up with practical solutions and preventive measures to fix the problem and stop it from happening again. These actions might involve improving processes, providing training, changing policies, or adjusting equipment or systems.
- Implement and monitor: Put the recommended corrective actions into action and keep an eye on how well they work. Follow up to make sure the solutions are in place and the problem doesn’t happen again.
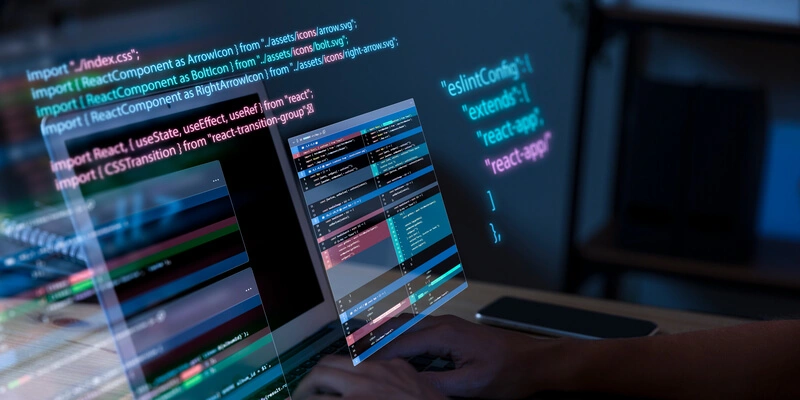
RCA Techniques
The 5 Whys technique involves asking “why” repeatedly to uncover the root causes of a problem by tracing its cause-and-effect chain. It’s a simple yet powerful method that helps teams dig deeper into the underlying factors.
The Fishbone Diagram, also known as the Ishikawa diagram or Cause-and-Effect diagram, visually represents potential causes and their relationships to a problem. It categorizes causes into groups like people, process, equipment, materials, and environment, aiding structured analysis.
Fault-Tree Analysis (FTA) is a deductive method that visually depicts events, probabilities, and logical connections to analyze failure or accident causes. It identifies combinations of events leading to the problem, prioritizing critical factors needing attention.
Pareto Analysis, based on the 80/20 rule, identifies and prioritizes significant problem causes. It focuses efforts on the vital few causes with the most impact, ensuring efficient resource allocation.
Change Analysis examines recent changes before the problem arose to uncover any modifications triggering the issue. It reveals causal relationships between changes and problems.
Failure Mode and Effects Analysis (FMEA) systematically identifies potential failure modes and their effects on systems, processes, or products. It evaluates risks by assessing failure severity, likelihood, and detectability, enabling preventive measures.
Statistical Analysis techniques like regression analysis and data mining identify correlations, patterns, or trends in data sets. They offer insights into potential root causes and their relationships to the problem.
These techniques are often used together for a comprehensive Root Cause Analysis (RCA), depending on the problem’s nature, available data, and team preferences. The goal is to accurately uncover root causes and develop effective prevention strategies.
The 8D (Eight Disciplines) approach is another problem-solving methodology incorporating RCA, commonly used in the automotive industry and other sectors. It provides a structured framework for problem-solving, collaboration, and continuous improvement.
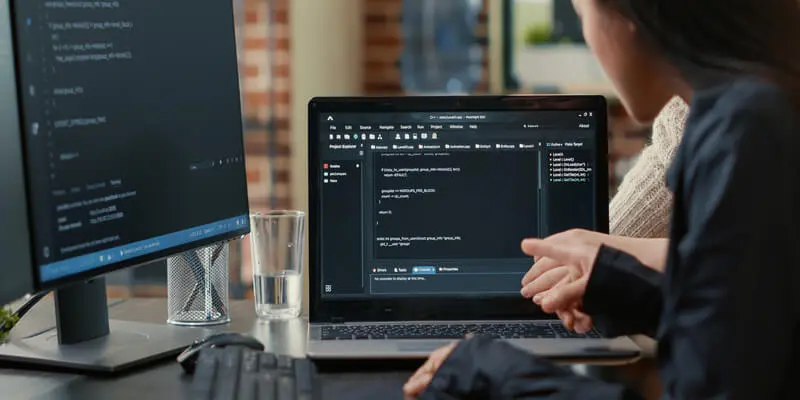
Here is an overview of the 8D process:
D1: Establish the Team. Assemble a cross-functional team with the necessary skills and expertise to address the problem effectively. Assign a team leader responsible for coordinating the process.
D2: Describe the Problem. Clearly define the problem, its impact, and any relevant background information. Use objective data and facts to provide a comprehensive understanding of the issue.
D3: Contain the Problem. Take immediate action to contain the problem and prevent it from escalating further. Implement temporary measures or workarounds to mitigate the direct impact.
D4: Identify the Root Cause. Conduct a thorough Root Cause Analysis (RCA) to determine the underlying factors contributing to the problem. Use techniques like the 5 Whys, Fishbone diagrams, or other appropriate tools to identify the primary root cause.
D5: Develop Corrective Actions. Based on the identified root cause, brainstorm and propose corrective actions that will eliminate or mitigate the root cause. These actions should be practical, feasible, and address the problem at its source.
D6: Implement Corrective Actions. Put the proposed corrective actions into action. Develop an action plan, allocate resources, and define responsibilities and timelines. Ensure effective communication within the team and across relevant stakeholders.
D7: Prevent Recurrence. Implement measures to prevent the problem from recurring. This may involve process changes, training, improved documentation, quality control checks, or other preventive measures. Consider incorporating mistake-proofing techniques to minimize the likelihood of future occurrences.
D8: Recognize the Team and Closure. Acknowledge the efforts of the team members and celebrate their contributions to solving the problem. Evaluate the effectiveness of the 8D process and document lessons learned. Close the 8D report and ensure appropriate documentation for future reference.
The 8D process encourages a systematic and disciplined approach to problem-solving, emphasizing collaboration, data-driven analysis, and preventive measures. It enables organizations to address issues comprehensively, minimize risks, and promote continuous improvement.
Conclusion
Root Cause Analysis (RCA) stands as a powerful method for identifying the root causes of organizational issues and failures. By going beyond surface-level symptoms, RCA enables organizations to implement effective corrective actions and prevent future occurrences. The systematic nature of RCA, along with the use of advanced tools like RCA software, enhances efficiency, collaboration, and data-driven decision-making. Incorporating RCA into problem-solving processes instills a proactive approach, allowing companies to tackle issues at their core and pave the path for long-term success. With RCA guiding their efforts, organizations can turn setbacks into opportunities for improvement, ensuring resilience and success in the future.
If you found this article helpful, make sure to follow the Elite Dev Squad blog for more insightful posts!
Related Articles
UX Design 2025: Make or Break Your Product
In a digital economy where milliseconds determine whether users stay or leave, UX has evolved from a “nice-to-have” to a bottom-line business strategy.
GPT Web Dominance
The emergence of Generative Pre-trained Transformers (GPT) has revolutionized the period of human-like content generation, transforming neural networks into a potent creative force.
Business and Technology
This is great advice from Forbes contributor Joe McKendrick.